Copper Matte
This is my favourite technique and is one in which it is technically quite difficult to achieve good results. The end result is always an unknown but will create wonderful mixtures of colours all from one oxide.
The technique begins with a special type of Raku clay which is heavily grogged, this means it has lots of coarse material contained within it to reduce clay shrinkage and prevent the pot exploding with thermal shock. There is a good article here if you want to know more about grog.
The copper matte pots I make start with a type of clay called Ashraf Hanna. They are formed into the shape I require on the potter’s wheel, and left to dry for about 7-14 days. Once dry ('leather hard') the pot is fired in an electric kiln to 980 degrees Centigrade. This process is known as a 'Bisque fire' and turns the pot into ceramic so instead of crumbling it would now smash if you dropped it. The Raku firing is the next step. The pot is coated in a mixture of copper oxide and water and left to dry before being placed into a gas-fired kiln and slowly heated to just over 1000 degrees Centigrade for about 45 minutes to an hour.
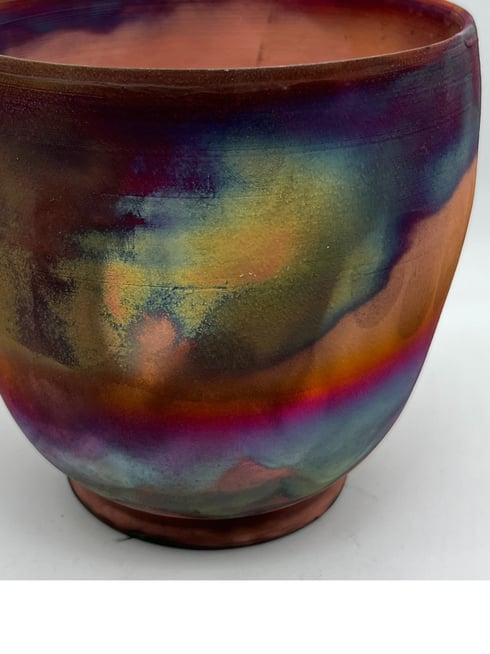
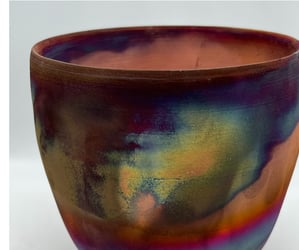
When at the correct temperature, the pot is removed from the kiln and placed onto a bed of shredded newspaper or anything organic and flammable. The temperature of the pot causes the newspaper to ignite and flames lick up the side of the pot for up to a minute.
A metal box is placed over the pot to extinguish the flames which in turn consumes the oxygen within the box. A minute or so later the metal box is lifted for less than a second and in this short period of time the oxygen rushes to the oxide glaze on the pot and causes it to burst into colour.
The box is replaced and all air holes at the opening are covered with sand to stop oxygen reaching the pot again. The slow motion video shows the colour changing in less than 2 seconds
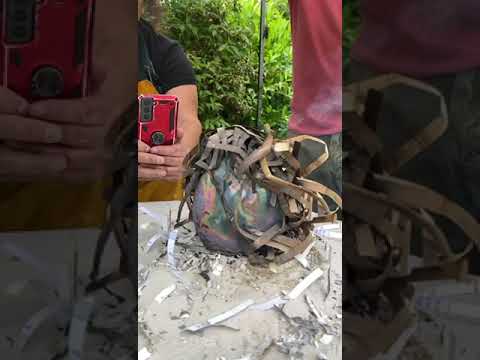