Naked Raku
This is a beautiful technique when done right. The end result is always exciting as you don’t get to see the finished product until you’ve scraped off all the glaze!
The technique begins with a special type of Raku clay which is heavily grogged, this means it has lots of coarse material contained within it to reduce clay shrinkage and prevent the pot exploding with thermal shock. There is a good article here if you want to know more about grog.
The Naked Raku pots I make start with a type of clay called Ashraf Hanna. They are formed into the shape I require on the potter’s wheel, and left to dry for about 7-14 days. Once dry ('leather hard') the pot is fired in an electric kiln to 980 degrees Centigrade. This process is known as a 'Bisque fire' and turns the pot into ceramic so instead of crumbling it would now smash if you dropped it. The Raku firing is the next step.
The pot is given two coats of glaze, the first is a very clay rich glaze which is designed to crack when fired, and the second is any crackle glaze I happen to have lots of, as it will ultimately be sacrificed during the firing.
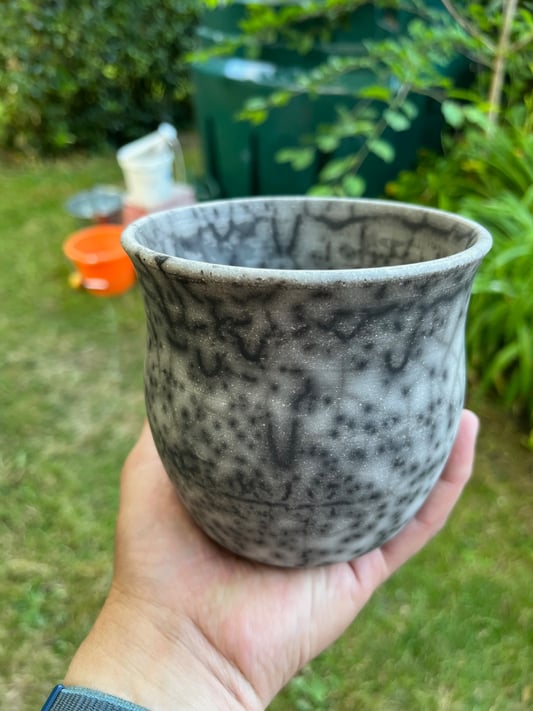
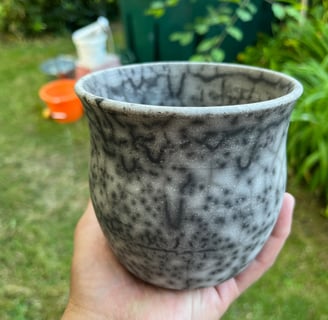
The clay glaze is applied followed by the crackle glaze, then the pot is left to dry before being placed into a gas-fired kiln and slowly heated to about 950 degrees Centigrade for about 45 minutes to an hour.
When at the correct temperature, the pot is removed from the kiln and placed into a metal container half filled with sawdust. The sawdust ignites when the pot is placed into it, and then a few seconds later the lid is placed on the container to quench the flames. After about 20 minutes the pot is removed from the smoke bin and cooled in a bucket of water.
As it cools the clay glaze begins to fall off the pot, bringing it back to its pre-glazed state, however whilst it was in the smoke box the smoke has permeated the 2 glazes and fills the cracks in the glaze, leaving smoke lines and dots all over the pot.