Crackle Glaze Raku
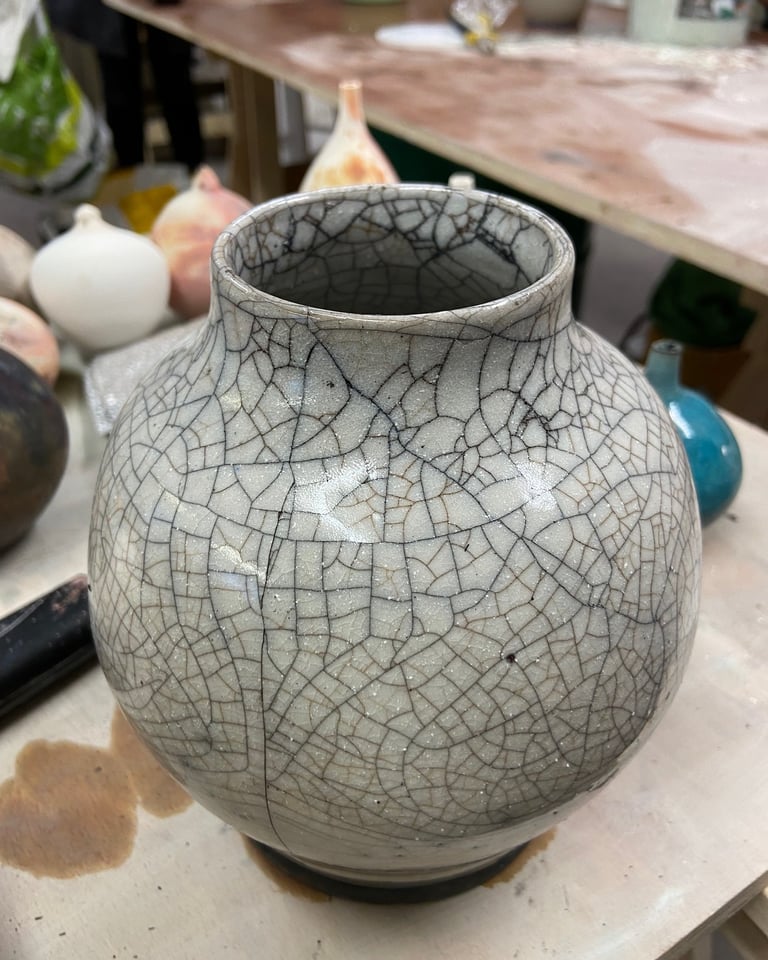
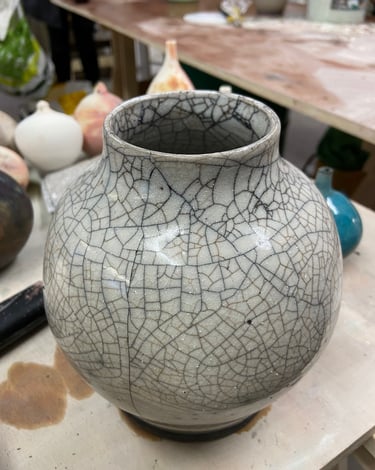
This is a beautiful form of Raku pottery with the finished pot having a lovely crackle in the glaze, sometimes with a metal shimmer to it.
he technique begins with a special type of Raku clay which is heavily grogged, this means it contains a lot of coarse material to reduce clay shrinkage and prevent the pot exploding with thermal shock. There is a good article here if you want to know more about grog.
The crackle glaze pots I make start with a type of clay called Ashraf Hanna. They are formed into the shape I require on the potter’s wheel, and left to dry for about 7-14 days. Once dry ('leather hard') the pot is fired in an electric kiln to 980 degrees Centigrade. This process is known as a 'Bisque fire' and turns the pot into ceramic so instead of crumbling it would now smash if you dropped it. The Raku firing is the next step. The pot is placed into a gas-fired kiln and slowly heated to about 950 degrees Centigrade for about 45 minutes to an hour.
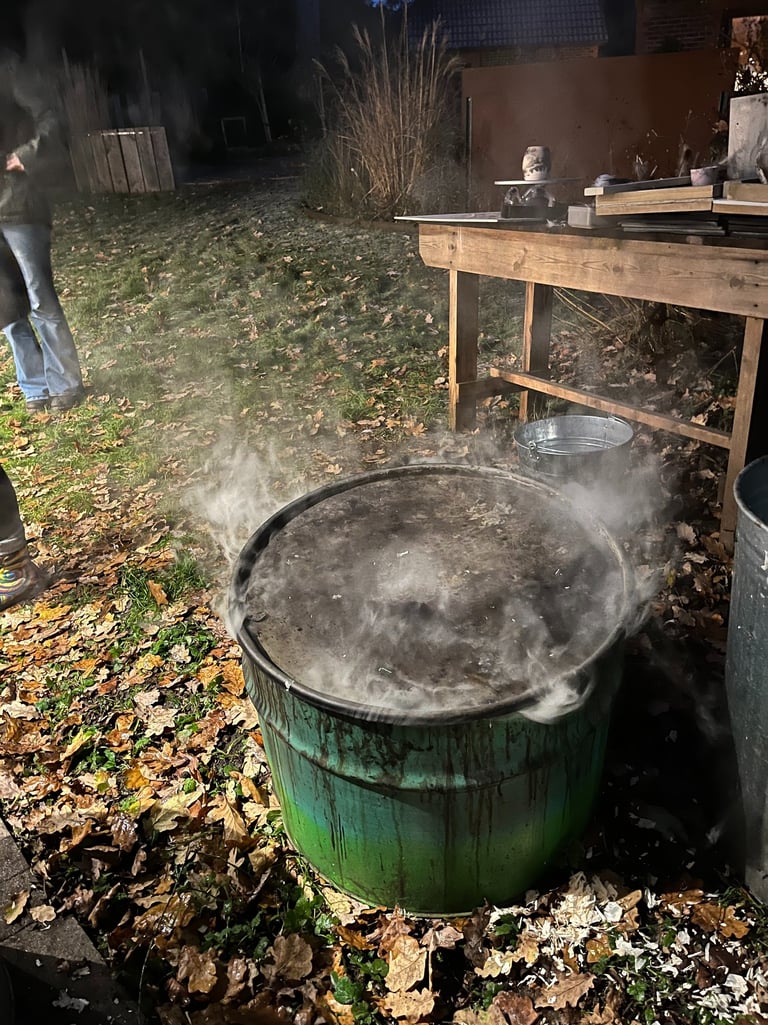
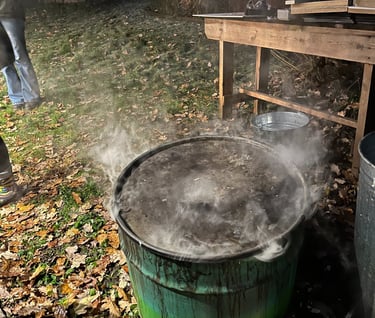
When at the correct temperature the pot is removed from the kiln and left in the air for a few moments to allow the crackle to form (the crackle is the glaze shrinking). It is then placed into a metal container (see above) which is half filled with sawdust. When the pot touches the sawdust it immediately ignites it, as it is still close to 950 degrees Centigrade at this point. The fire in the metal container is extinguished by placing an air tight lid onto it. Once the fire is put out, the smoke in the container seeps between the crackle making the crackle lines black. After 20 minutes the pots are removed from the smoke bin and quenched in cold water to cool them.
If a metallic finish is required then the pot is not left in the air after leaving the gas kiln, and is instead immediately placed in the smoke bin and the lid put on straight away. This creates a 'reduction' environment where the oxygen is used up by the flames and the oxides in the glaze come to the surface as shiny metallic patches.
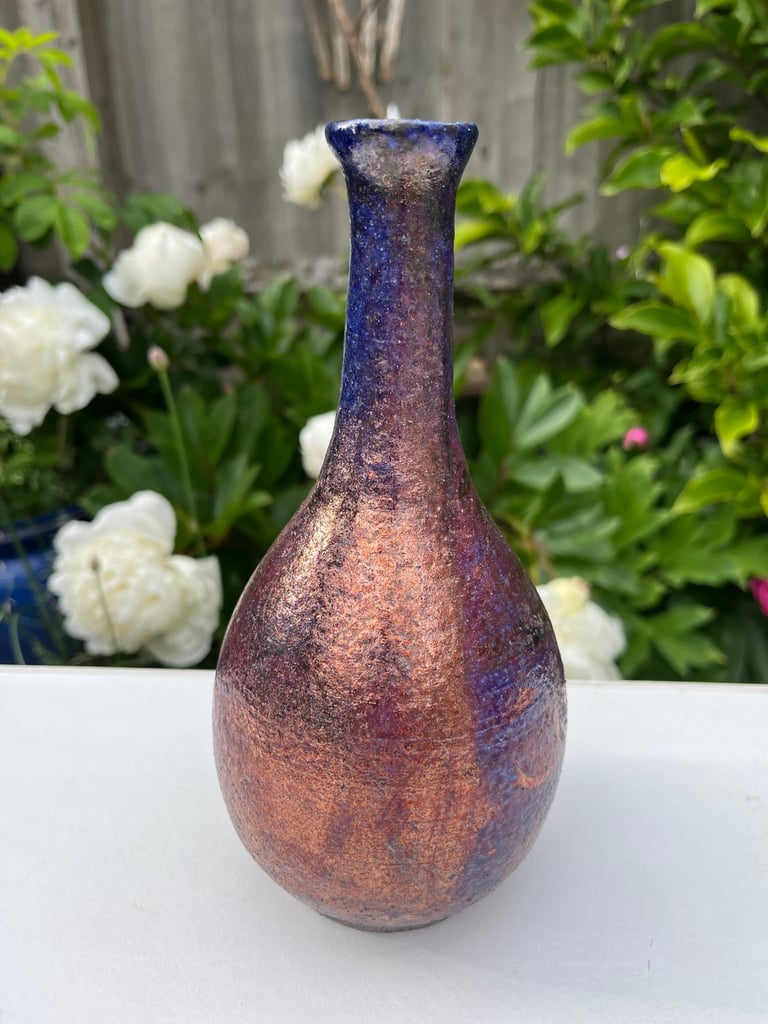
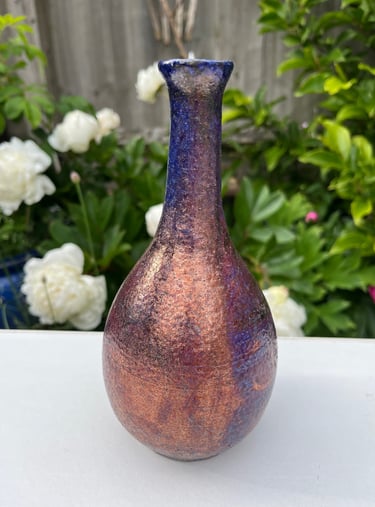